Decreasing Oil Reserves, Unstable Sources, Volatile Prices
In 2005, a US Department of Energy report estimated that 110 million barrels of crude oil remain in the ground in wells where extraction produced 10 barrels a day or less. Approximately 400,000 of these marginal stripper wells produce nearly one million barrels of oil per day 19% of U. S. production. About 142,000 stripper wells were plugged and abandoned from 1994 to 2003, costing the United States in excess of $3.8 billion in lost oil revenue at the Energy Information Administrations reported 2004 average world oil price. Although the well closure trend has slowed, primarily due to the high oil prices of the past several years, reactivating these wells remains very expensive.
The amount of oil remaining in marginal stripper wells may seem relatively small when viewed individually, but taken collectively it is a resource wellspring. Large numbers of retired oil wells across the U.S. have been capped, with the equipment disassembled and redeployed. The volatile price of oil and the unstable oil markets have made it essential to utilize these resources in order to access otherwise lost oil revenue thereby decreasing dependency on foreign oil.
From Expensive Conventional Pumps to Low-cost Lift System
New-on-the-scene in 2006, Charles Ice, founder and President of Fifo Technologies, Inc., conceptualized, developed and produced an artificial lift that could replace the expensive traditional pumping technology for extracting oil from stripper wells. His lift offered the oil industry a system with a low enough capital outlay for purchase, installation and maintenance that it could be economically feasible for oil companies to convert dormant wells into oil producers.
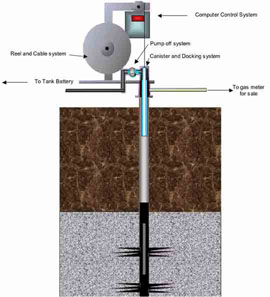 |
Figure 1: F1000 Artificial Lift System |
Ices innovative F1000 Lift System (See Figure 1) involves an on board computer program that monitors and executes the operational se
quence. A command is issued that sends the canister down the well bore. When the canister contacts the surface of the fluid, the fluid level is noted and logged. Then, when the set point for depth is reached, a dwell timer activates and the canister begins to fill. When full, a command returns the canister and the fluid is evacuated and sent to the Tank Battery.
The Fifo F1000 system provides a low cost, state of the art solution for marginally producing oil wells in the 1/2 to 3 barrels per day category at a depth of 3000 feet. Additionally, the F1000 has no down hole parts, it therefore requires no special equipment for maintenance or repair.
From No Real-time Monitoring to Automated Continuous Monitoring, Control and Reporting
Unlike the conventional or jack pump that require on-site maintenance and monitoring, the F1000 has the capability to remotely log and report data as well as monitor and control production and operation, significantly lowering extraction costs by 65% to 80% over conventional pumping methods. For the data transfer module of his system, Ice, selected the robust, long-range wireless Ethernet modem from Data-Linc Group and worked with The Reynolds Company (TRC of Dallas, Texas), the local distributor for Data-Linc products. For the SCADA (Supervisory Control and Data Acquisition) system component, Reynolds recommended the Allen-Bradley MicroLogix 1100. Fifo , Data-Linc Group and Reynolds cooperative effort resulted in a network design that seamlessly interfaced pump, data-communication equipment and PLC (Programmable Logic Controller) into a reliable, economical network solution for tapping the thousands of abandoned stripper wells.
Each Fifo unit includes the F1000 lift system, an Allen-Bradley MicroLogix 1100 and a Data-Linc SRM Ethernet radio modem. The MicroLogix is a smart component that can be programmed to monitor and control what is happening at the Remote station and report that data to central control.
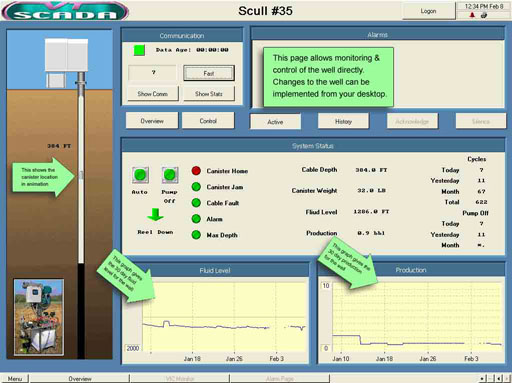 |
Figure 2: Fifo SCADA display providing pumping operation information and system status from any PC anywhere |
From Limited On-site Checks to Remote, Real-time Monitoring, Control and Reporting
Data-Lincs 900 SRM MHz wireless Ethernet modem transfers the data between the MicroLogix at the well site and the SRM modem connected to the PC at the control center for real-time monitoring and control with the capacity to program the MicroLogix 1100 PLCs anywhere on the network. This means, from any PC anywhere, the Fifo system can continuously monitor and control pump activityfor continuous fluid level monitoring, daily well production records and well-gas capture for delivery to flow-lines without special software or costly communication systems (See Figure 2). Fifos F1000 system provides critical communication but requires no cables between well pumps and storage tanks and thus avoids expensive trenching and the recurring cost of leased lines.
Additionally, the SCADA software provides reports and electronic data logs associated with the production of the wells well bore fluid level, number cycles vs. number of pump offs, current set point and current oil production, etc., all of which may be forwarded to a secure web site. These features allow those involved or responsible for the project to have access to production records and operational data as needed and in real-time. The various reports can be down loaded into spreadsheets and printed or viewed online from any location. (See Figure 3.)
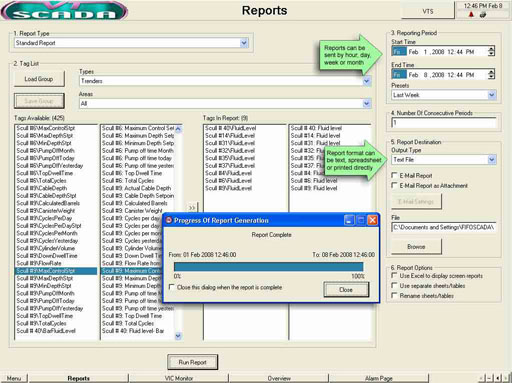 |
Figure 3: Data may be transferred to spreadsheets and used to generate reports. |
|